Muscles made of plastic
Biological processes for movement have been developed through evolution over millions of years, and are thus often significantly complicated. Man-made machines, on the other hand, are definitely both more powerful and faster than many biological counterparts, but their simplicity renders them less universal. Compare, for example, a bird to an airplane: while the plane can fly longer and at higher speed, it cannot reproduce the elegance, precision and fast manoeuvring of an eagle. Or take a look at the underwater world: the fascinating way a dolphin can jump out of water is still extremely out of reach with our present engineering possibilities. At the same time, mankind has since the beginning of civilization been able to invent and construct new technology, also without reproducing nature. One formidable example is the wheel: this type of rolling motion is very rare in nature. If we can combine the engineering and architectural spirit of humans with the inspiration of biological systems, a whole new world of technology would open up. The key here is new materials, which can replace today's metal wheels, propellers, bars, and pistons. Natural materials are superior in terms of compactness and flexibility.
Contemporary mobility devices are based on motors. A conventional motor create a rotating movement, which is then transferred to the wheels. Another popular mode of movement is bases on propulsion, which is the basis for a jet engine. To a lesser degree, so called linear actuators have been used in contemporary technology. These are today mainly used to adjust the controlling devices of surfaces, wings or propeller blades. However, the simplicity of actuators makes it possible for them to be fundamental in future mobility devices. A small voltage put over the material causes it to bend or to contract - very similar to an animal or human muscle.
Building devices based on these elements gives us the possibility to construct artificial muscles.
During the last decades, materials scientists have been working on exploring electromechanically active polymer materials (EAPs), i.e. polymer materials which can shrink or bend under electrical stimulation. Polymers are basically plastics - long, chainlike molecules which are cheap and easy to synthesize in large quantities. Being noiseless, soft, flexible and light-weight, EAPs have many potential applications in the areas of noise damping, smart textiles, biorobotics or medicine. Some are also biologically compatible, making it possible to develop medical devices which can help surgeons to use less invasive medicine. For example, EAP devices may help to deliver drugs in very exact amounts or into very specific locations in the body (such as tumours).
There is yet one more promising property of these EAP actuators: they are easily miniaturized. This is a necessary feature if one would like to build complex devices consisting of thousands of different elements moving in an organized fashion. Imagine how complicated is to develop a 0.1-mm-size motor. Although it possible to construct such an apparatus, it must be done in a complex science facility and needs a lot of engineering expertise. The development of such EAP-based actuator on this small scale, on the other hand, can easily be done in any chemistry lab. Moreover, it will soon be possible to fabricate micro-actuator devices in large quantities by using microfabrication techniques, making these devices accessible to everyone.
There are two main types of EAPs. First are the so-called electrostatic polymers. In order to make them actuate - i.e. to contract - they should be charged by a high voltage. As a result, opposite charges in the material will attract each other and it will shrink. Applications, such as water pumps and electrical generators, are in the near horizon for these materials: however, the high voltage used creates serious problems in medical or biological applications. Therefore, much interest is instead directed towards ionic EAPs, which are based on ion migration when an electric field is applied over the material. These operate using under a few volts. They possess some drawbacks in terms of actuating speed and force properties, but these problems have become less severe with scientific achievements in recent years. Several research groups are developing robust, easy-to-make, fast and strong actuator materials. Today, there are materials available which can bend more than 200 times per second, and materials which can move hundred times their own weight. We have achieved unique results by using specific fine-tuned nano-porous carbon powders as electrode materials.
There is no limit to the future applications of such artificial muscles. They can be used as prosthetics, for man- or animal-like robots, as extra limbs, or as 'smart additions' to existing devices. We can certainly use artificial tails, extra arms or fingers for precision or multi-tasking. Science will then provide less of an obstacle when realizing science fiction.
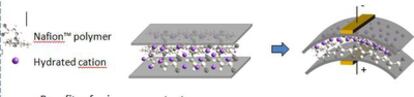
Tu suscripci¨®n se est¨¢ usando en otro dispositivo
?Quieres a?adir otro usuario a tu suscripci¨®n?
Si contin¨²as leyendo en este dispositivo, no se podr¨¢ leer en el otro.
FlechaTu suscripci¨®n se est¨¢ usando en otro dispositivo y solo puedes acceder a EL PA?S desde un dispositivo a la vez.
Si quieres compartir tu cuenta, cambia tu suscripci¨®n a la modalidad Premium, as¨ª podr¨¢s a?adir otro usuario. Cada uno acceder¨¢ con su propia cuenta de email, lo que os permitir¨¢ personalizar vuestra experiencia en EL PA?S.
?Tienes una suscripci¨®n de empresa? Accede aqu¨ª para contratar m¨¢s cuentas.
En el caso de no saber qui¨¦n est¨¢ usando tu cuenta, te recomendamos cambiar tu contrase?a aqu¨ª.
Si decides continuar compartiendo tu cuenta, este mensaje se mostrar¨¢ en tu dispositivo y en el de la otra persona que est¨¢ usando tu cuenta de forma indefinida, afectando a tu experiencia de lectura. Puedes consultar aqu¨ª los t¨¦rminos y condiciones de la suscripci¨®n digital.